+86 17307552869
yanyan@yanmisz.com
Selective Laser Sintering 3D Printing Service
Upload your CAD files, receive an instant FDM 3D printing quote and get your parts into production in less than 5 minutes.
🔒 All uploads are secure and confidential

Our SLS 3D Printing Service
From prototyping to small-batch production, for you to produce highly accurate parts with quality and strength comparable to injection molding.
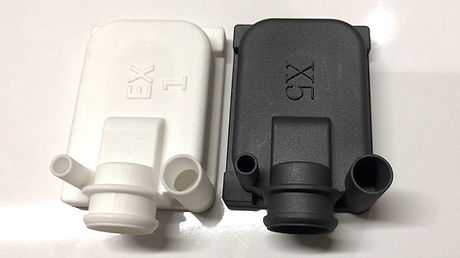
Standard capabilities | Description |
---|---|
Materials | Nylon 12 (PA 12), Glass-filled Nylon (PA 12 GF) |
Lead time * | 3 business days
|
Dimensional accuracy | ± 0.3% with a lower limit of ± 0.3 mm (± 0.012”)
|
Layer thickness | 100 μm |
* For expedited lead times or parts that exceed the maximum build size contact yanyan@yanmisz.com.
Available Materials for SLS 3D Printing
Nylon 12 (PA 12)
SLS nylon is a robust thermoplastic with all-around excellent physical properties, ideal for functional prototypes and end-use applications.
Type: Markforged Onyx
Strengths: No support material required, Excellent mechanical properties, Can produce complex geometries
Weaknesses: Higher cost than FDM, Longer lead times than FDM
Wall Thickness: 0.7 mm
Tolerances: ±0.3% with a lower limit of ±0.3 mm (±0.012″)
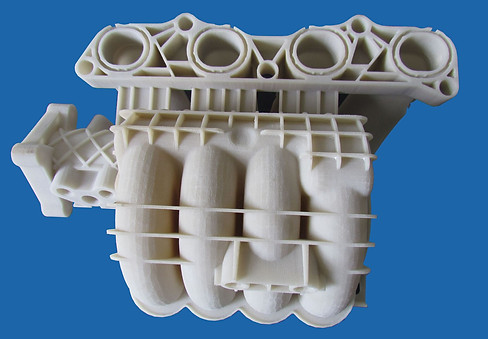
Available Surface Finishes for SLS 3D Printing

As printed
As printed SLS parts are typically white or stone grey in color with a smooth surface and a powder texture and without visible layers.

Dyed (black)
SLS parts are dyed black by immersion in a warm color bath. The color penetration reaches a depth of about 0.5 mm and covers all surfaces.

Spray painting *
SLS parts can be painted white, black or in a specified RAL or Pantone color.
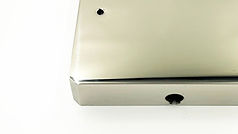
Tumble smoothing *
SLS parts are dyed black by immersion in a warm color bath. The color penetration reaches a depth of about 0.5 mm and covers all surfaces.
* These finishes are available by contacting yanyan@yanmisz.com.
Ideal SLS Applications
Recommend using SLS for the following use cases.

Functional Prototyping
SLS is ideal for fabricating functional prototypes from durable, chemically resistant engineering thermoplastics.
Requirements
Strength: Medium/High
Appearance: Smooth surface
Quantity: 1-5 parts
Low-volume Production
SLS is cost-competitive to injection molding for low-volume manufacturing of end-use plastics parts for quantities up to 300 units.
Requirements
Strength: Medium/High
Appearance: Injection molding-like
Quantity: 10-300 parts
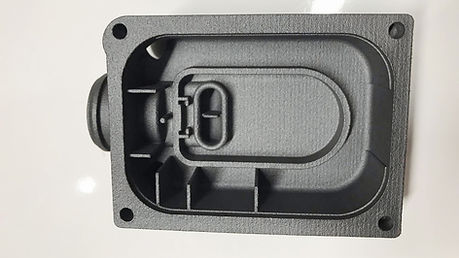
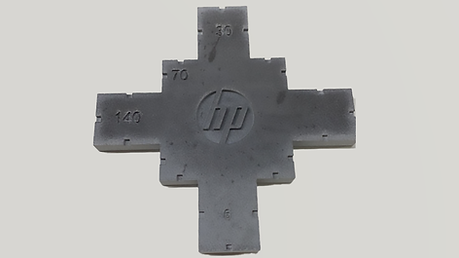
High-performance Components
SLS can produce optimized parts from advanced polymer composites that can be used as replacements to metal components.
Requirements
Strength: High
Appearance: Smooth surface
Quantity: 1-50 parts
Design Guidelines for SLS
The table below summarizes the recommended and technically feasible values for the most common features encountered in 3D printed parts.
Feature | Recommended size |
---|---|
Unsupported walls | 1.0 mm (0.040'')
|
Supported walls | 0.8 mm (0.031'')
|
Minimum detail size | 0.8 mm (0.031'')
|
Minimum hole size | 1.0 mm (0.040'') |
Moving parts | 0.5 mm (0.020'') between moving surfaces
|
Assembly clearance | 0.4 mm (0.016'') between mating surfaces |
Maximum wall thickness | 20 mm (0.8''). Thicker parts must be hollowed with and at least two escape holes for powder removal with a min. diameter of 8 mm (0.3''). |
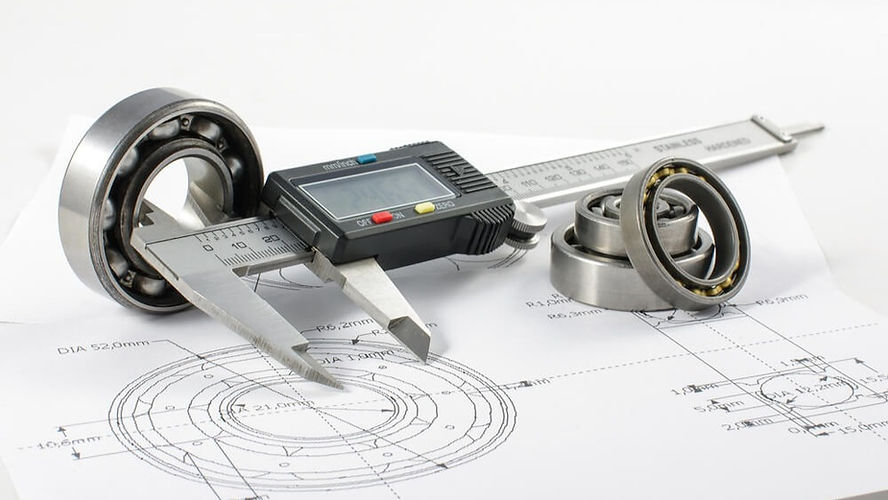
Design Recommendations
If using 3D printing for higher part quantity fabrication (20+), SLS will be the most cost-effective additive manufacturing process.
-
For long, thin parts: use ribbing to mitigate warping risks.
Requirements
Gaps for Mating Parts: 0.5 mm clearance between features
Tolerance: +/- (0.25 mm + 0.002mm/mm)
Min Wall Thickness: 1.0 mm for production, 1.5 mm for consistent measurement or mechanical properties